With labor issues continuing to stress the construction industry, autonomous construction machinery and robots displayed at CONEXPO-CON/AGG 2023 generated a lot of excitement. According to The Business Research Company, the global autonomous construction equipment market will grow from $14.05 billion in 2023 to $20.33 billion in 2027, at a compound annual growth rate (CAGR) of 9.7%. Here’s a review of how these autonomous machines and robots hope to solve labor and safety issues for the construction industry. It’s a matter of finding the applications where autonomy can work well.
Solar pile driving
Built Robotics RPD 35 Autonomous Pile Driver
Built Robotics has been converting excavators into autonomous robots with its Exosystem since 2019, but recently turned its attention to the RPD 35, a fully autonomous solar pile driving system. According to Erol Ahmed, Corporate Communications Director, the RPD 35 is currently being piloted with several EPC contractors.
“They want this product,” says Ahmed. “We are anticipating it will be three to five times faster than traditional methods.” On a utility-scale solar installation, there are typically four steps in pile installation: surveying, distribution, pile driving, and as-builts. The RPD 35 robot automates that four-step process to be handled by one machine.
The product includes a base excavator with a unique sled carrying system that can hold up to 192 piles and a custom-designed driving attachment that picks up the piles and drives them into the ground. One robotic equipment operator (REO)can run from 1 to 3 machines. To make it easier for contractors to adopt its autonomous equipment, Built products are available through a robotics as a service rental model. Commercial deployments of the RPD 35 are scheduled for early 2024.
With solar energy becoming the cheapest and fastest growing energy source in the United States, Built has plans to develop solutions for other aspects of solar energy construction with the goal of providing autonomous solutions for all parts of the solar farm lifecycle: earthmoving, installation, and maintenance. Earlier this year it purchased Roin, a three-year-old engineering company that has designed and built several robotic concrete finishing solutions, including a shotcrete robot and a concrete troweling robot. The acquisition has helped accelerate Built’s entry into more diverse autonomous offerings.
Solar installations
Sarcos Guardian® XM and an Autonomous Delivery Vehicle
Sarcos Technology and Robotics Corporation recently completed final validation of its Outdoor Autonomous Manipulation of Photovoltaic Panels (O-AMPP) project. During this field trial, which began in 2021 with funding support from the U.S. Department of Energy Solar Energy Technologies Office, Sarcos developed a harmonized robotic system to deliver, detect, lift, and place photovoltaic modules in the field. The system consists of a Guardian® XM robotic system, and an Autonomous Delivery Vehicle (ADV). Sarcos expects to commercially launch its robotic solar field construction solution in 2024.
Watch the video here and learn why the solar industry needs autonomous solutions.
Material delivery
Honda Third Generation Autonomous Work Vehicle
American Honda Motor Company introduced its third-generation, autonomous work vehicle (AWV) at CONEXPO-CON/AGG 2023. Designed to support construction-related activities and enhance workforce productivity, the AWV can be operated manually or via remote control. The Honda AWV employs a suite of sensors to operate autonomously, using GPS for location, radar, and lidar for obstacle detection, and cameras for remote monitoring. Previous field tests have successfully verified that multiple Honda AWVs can transport and deliver construction materials and supplies at precise points along a pre-set route. The latest version of the vehicle boasts a wider bed, greater loader capacity (up to 2,000 pounds) improved navigation in areas of weak GPS signals, higher speeds (up to 10 mph in autonomous mode), and extended battery life (up to 10 hours).
Rebar work
Advanced Construction Robotics (ACR) launched its second product, IronBOT, during CONEXPO-CON/AGG. IronBOT augments construction crews by lifting, carrying, and placing up to 5,000-pound bundles of rebar in a transverse or longitudinal orientation without the need for heavy lifting from crewmembers. When IronBOT is combined with the company’s TyBOT, a rebar-tying robot, the company says customers can typically provide 50% schedule savings during rebar installation.
Hauling
Bell Equipment has partnered with Pronto AI on an autonomous articulated dump truck. First introduced in 2021, the system uses cameras mounted on the truck to observe the road and job site environment. It then feeds that data into neural networks that analyze every image in conjunction with other inputs to make optimal driving decisions. According to the company, benefits include lower operating costs, safer worksites, and lower daily maintenance costs. The machines can work with consistency 24/7.
Utility detection and marking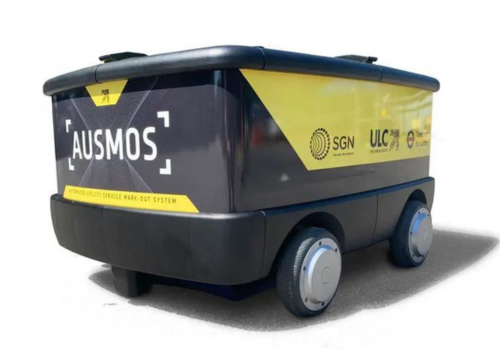
AUSMOS, from ULC Technologies, is a semi-autonomous robotic platform that detects and marks-out below-ground infrastructure utilizing a sensor suite comprised of ground penetrating radar (GPR) and electromagnetic sensors. The robotic platform automates underground mapping enabling denser GPR data collection and more powerful post-processing techniques that result in easier-to-interpret data, reducing the risk of accidental damage to buried assets. The company currently has pilot programs in the U.S. and the U.K.
Autonomous lifting and loading
With its concept machine, RogueX, Bobcat explores autonomy and electrification in one platform. “It was an opportunity to learn, explore and test with customers to see what their reactions were,” says Joel Honeyman, Vice President of Global Innovation for Bobcat. According to Honeyman, reaction to the machine was positive, with customers revealing what applications they might have for the machine. Some of the applications where Bobcat envisions the vehicle working include in a barn around animals, interior demolition, interior clean-up, and waste transfer stations.
Without an operator station, engineers were able to completely redesign the lift arm, to allow for 24 more inches of reach at the top of the dump. “Because we're able to center that linkage, rather than using the outside of the machine around the cab, our engineers created a unique lift arm design that allows the machine to have way more reach,” says Honeyman.
According to Honeyman, some of the technologies incorporated into the machine will be finding their way into other machines. The company is planning for a limited production launch of an autonomous mower in late 2023.
Honeyman believes a lack of skilled labor will be one of the driving forces for increased automation. “Technology can help make new operators more efficient and more productive faster.” He also thinks customers are going to have to see the technology in action and experience it to believe it. “Once people experience these machines in the field, they will start saying ‘I can use it for this task,’” says Honeyman.
Will supervised autonomy take off first?
Teleo, which builds autonomous technology for heavy construction equipment, is banking on an incremental approach to autonomy with its system, called Teleo Supervised Autonomy, which enables remote and semi-autonomous operations of any make and model of heavy construction equipment. A key benefit is that one operator can control multiple machines from the comfort of a command center. The company recently announced agreements with construction customers John Aarts Group, Teichert, and Tomahawk Construction for remote-operated wheel loaders, bulldozers, and dump trucks.
Considerations when choosing an autonomous machine
Full autonomy is an extension of the automated features you may already be familiar with on construction equipment such as grade control. As machines become automated operators will become more trusting of the technology. If you decide to introduce an autonomous machine to your jobsite, Built’s Ahmed recommends keeping everyone aligned with what the robot is doing and how it will change current workflows. “Robots are efficient and likely to change how you sequence work on the jobsite,” he says.
Safety is the No.1 consideration with autonomous machines. If the machines can’t be operated safely, productivity benefits will matter. Autonomous machines have the potential to be safer because there is no operator, and a machine’s 360-degree visibility is better than a human operator.
Haldeman expects it will be five to 10 years for autonomy to take hold across all applications, but as our examples show, more simplified applications are already being introduced. It’s not too early to start thinking about how autonomy could benefit your operations. Robots and autonomous machines will be at a jobsite near you sooner than you think.
Read Next
Improving Jobsite Productivity with Technology